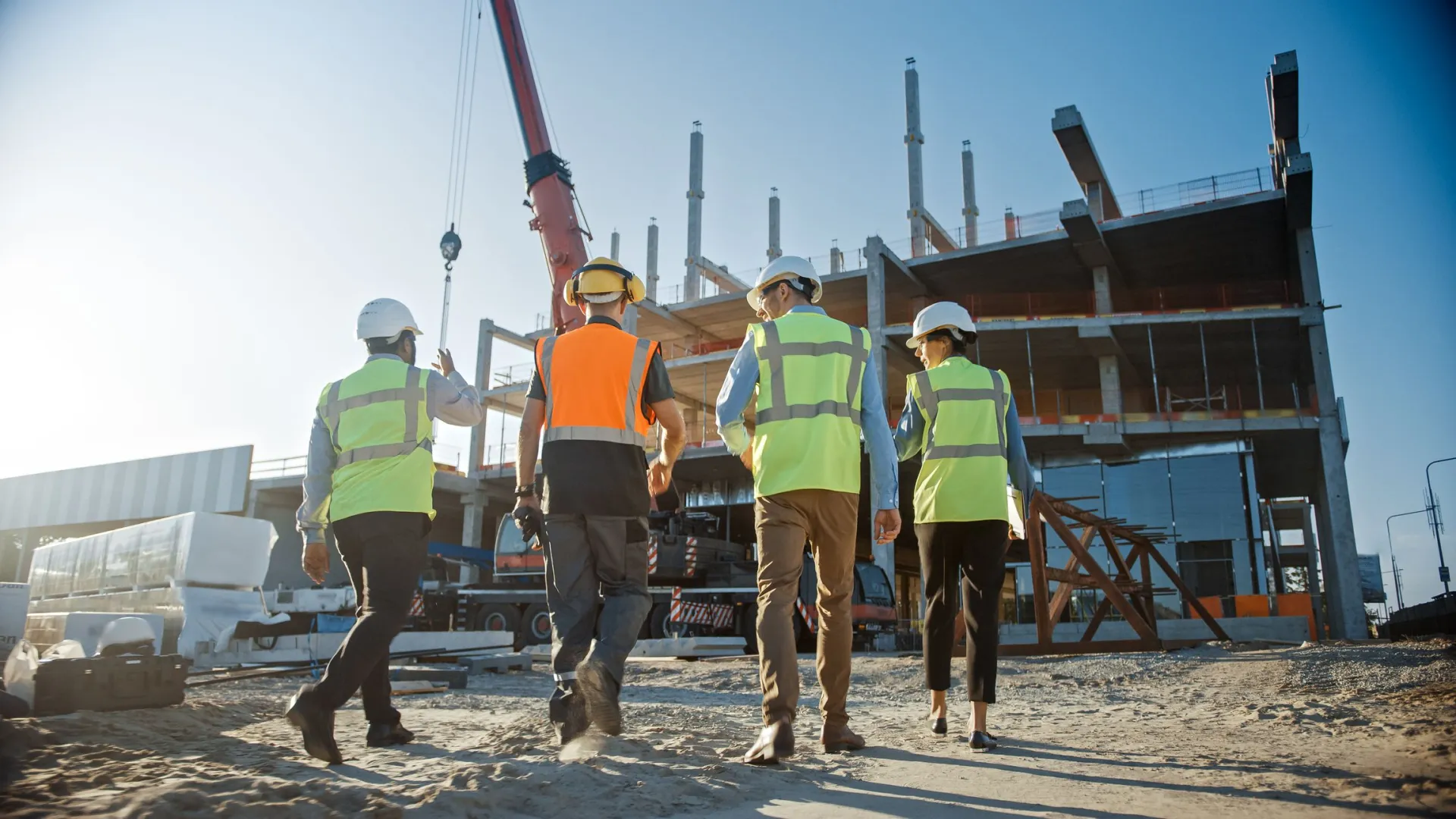
Safety Program
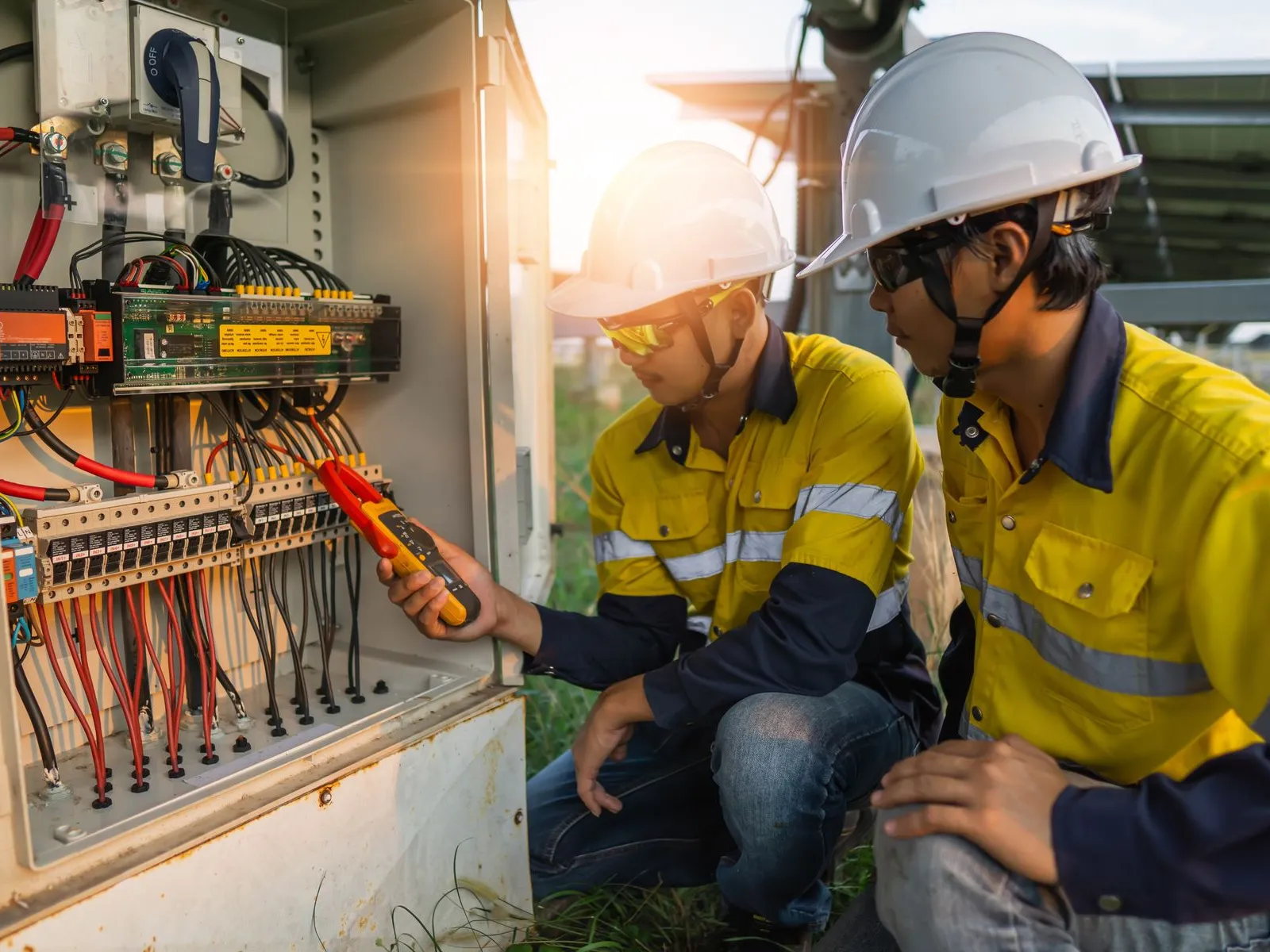
Training
All of our field employees go through the "Construction Safety Basics" training program with J. J. Keller & Associates, the nation's leading provider of safety and regulatory compliance solutions. The Construction Safety Basics curriculum (Work Practices, Work Environment, Safe Use of Equipment, & In Case of an Emergency) provides employees with a high-level overview of many construction safety topics. Specifically, it covers an introduction to safe work practices, various engineering controls that can be used to create a safe work environment, the safe use of tools and equipment, and what an employee should do in the event an emergency occurs.
Safety Awards
As a participating member of the Associated Builders & Contractors of Georgia, Sluss + Padgett measures our safety processes and policies using the STEP benchmarking tool. This safety benchmarking & improvement tool uses 25 key safety components that allow us to implement and enhance our safety program while reducing jobsite accidents.